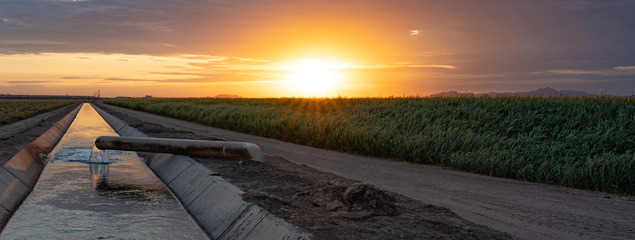
Increasing Irrigation Efficiency
Tools and Resources
LincSys
LincSys is a computer program for simulating the hydraulics of linear-move and center-pivot irrigation systems developed by Dr. Dawit Zerihun and Dr. Charles A. Sanchez. The name LincSys is a mnemonic for the phrase ‘linear-move and center-pivot systems’, two of the most important and widely used irrigation application methods. LincSys takes into account the effects of span geometry and key lateral components (namely, prvs and drop-tubes) on the system hydraulics and also has sufficient flexibility to accommodate variabilities in lateral hydraulic parameters and field topography.
At the core of the LincSys software is a pair of executable files: a hydraulic simulation module, HydrSimLaterals.exe, and a graphical user interface (GUI), LincSys.exe, through which the user interacts with the hydraulic module.
The GUI of LincSys consists of a tabbed form with four windows, namely, the Systems-Projects, Input, Output, and Charts tabpages. Each tabpage provides access to a set of program functionalities, consisting of project management, preprocessing, processing, and postprocessing of project data. Note that the term project is used in LincSys to refer to all the input and output data files (of a simulation problem) stored in a folder that bears the name of the project.
The help utility of the LincSys software provides resources that the user can tap into through tooltips, a dedicated Help menu that can be activated from the Systems-Projects window, and a set of text files placed in various folders during program installation.
The hydraulic module of LincSys, HydrSimLaterals.exe, is a numerical model that solves the continuity and energy balance equations (for one-dimensional steady flow through a branched hydraulic network consisting of straight and stationary pipes) to determine the lateral-wide distribution of link discharges and nodal heads and an array of additional output parameters. The model can be used to determine the hydraulic performance of a linear-move or center-pivot system that uses the following emission devices to meter outlet discharges along the lateral:
drop-tube, pressure regulator, and emitter assemblies,
drop-tube and emitter assemblies, or
emitters placed directly on the lateral.
The user interface and the computational module are coupled through an application programming interface. Data exchange between the user interface and the simulation module takes place through text files.
Resources
- Quick Introduction (PDF) and Quick Introduction (PPT): enables access to a document that presents a quick introduction to the LincSys software.
- User Manual (PDF): Provides access to the user manual of LincSys, a document that presents a detailed description of the core software components (LincSys.exe and LatHydrSim.exe) and capabilities; user interface layouts, features, and functionalities; how to install and run the software; the data file management and directory structure of the software; and results of model evaluation and simulation examples.
- Keyboard Usage Guide (PDF): Provides guidance on keyboard usage in LincSys.
System Importance
Center-pivot and linear-move systems are used to irrigate a wide variety of crops under a range of conditions (Gregg, 2004). These systems account for about half of the irrigated acreage in the U.S. (FRIS, 2008) and are expanding. With application efficiency exceeding 80% and coefficient of uniformity greater than 0.85 (Keller et al., 1980), linear-move and center-pivot systems can be considered among the most efficient irrigation methods.
High-pressure impact sprinklers were commonly used in the early versions of center-pivot systems (New and Fipps, 2018). However, because of energy costs and efficiency considerations, impact sprinklers are now recommended only in special applications such as land application of wastewater. More closely spaced low-pressure spray nozzles coupled to pressure regulators and drop-tubes are often used in recent systems (both center-pivots and linear-moves) to minimize energy consumption and wind drift and spray evaporation losses. Mainly because of their amenability to automation these systems are considered particularly suitable for site-specific application of water and agricultural chemicals and have minimal labor requirements.
Center-pivots are much more widely used in the U.S. than linear-move systems. Linear-move systems generally have higher initial cost per unit area of irrigated land, higher labor costs, and the need for a separate guidance mechanism (Martin et al., 2007). Furthermore, linear-move systems are suitable only for terrains with moderate and gentle slopes, not exceeding 3%, while center-pivots can be used in fields with gently rolling terrains and steeper slopes. Potential complexities associated with water intake apparatus, especially when water is supplied through an underground pipeline is another limitation of linear-move systems compared to center-pivots.
Linear-move systems, nonetheless, have some advantages over center-pivots, including the capability to fully irrigate a square field without the need for additional accessories at the far-end of the system, the capability to irrigate rectangular fields, and to maintain low application rates over the entire lateral length.
System Description
A linear-move or a center-pivot irrigation system is a self-propelled machine consisting of a steel or aluminum lateral that apply water to crops in the form of precipitation, as it moves across the irrigated field. Linear-move systems travel in a straight-line irrigating a rectangular field. Center-pivot systems, on the other hand, rotate about a pivot point fixed to a permanent base and irrigate a circular area, although various accessories can be used to irrigate parts of the field corners. Figure 1 depicts an aerial view of a linear-move or center-pivot system applying irrigation.
Linear-move and center-pivot laterals are generally placed at a suitable above-ground clearance atop an elevated platform, consisting of structural elements (trusses, cables, and support towers on wheels), drive units, and alignment mechanisms that support and propel the system as well as keep it aligned. Linear-move systems also require a separate guidance system that keeps it on course along a set travel direction during irrigation.
A sketch of a typical linear-move system, obtaining its supply from a canal, with an intake apparatus, a pump, and a power unit attached to its inlet-end is depicted in Figure 2a. The lateral is comprised of a series of arched spans connected, at their lowest points, with flexible joints that allow relative movement between adjoining spans. Each span has multiple regularly or variably spaced outlet ports.
Although high pressure impact sprinklers placed directly on the lateral outlet ports were used in early versions of center-pivots, recent machines (both center-pivots and linear-moves) typically use more closely spaced low-pressure spray nozzles to meter outlet discharges along the lateral. These systems often use semi-flexible tubing (known as drop-tubes) to convey water from outlet ports down to emitters, which are suspended at a constant above ground clearance (often under the crop canopy so as to minimize droplet wind drift and evaporation losses). The spray nozzles are typically combined with accessories known as wear panels (which are fixed or rotating) to produce a range of precipitation patterns that may suit different applications.
A curved rigid tubing, called a gooseneck connector, is used to connect each outlet port on the lateral with a drop-tube. Drop-tubes can be fitted with pressure reducing valves, prvs (Figure 2b). Some systems have prvs installed at the inlet-end of the drop-tube. Other systems have prvs placed at the lower end of the drop-tube, just upstream of the emitters (Senninger, 2017a). In the system considered in the LincSys software, it is assumed that prvs are placed immediately upstream of emitters.
As noted earlier, the use of precision applicator (droptube-prv-emitter) assemblies as emission devises to meter outlet discharges across a lateral at a preset rate has multiple advantages, including high irrigation uniformity and efficiency, a more uniform application of plant nutrients and other agricultural chemicals, and reduced energy consumption. These systems are also particularly suitable for variable application of water and agricultural chemicals.
A center-pivot irrigation system equipped with precision applicators is depicted in Figure 2c. Figure 2 shows that the structural elements, hydraulic components, and geometric features of center-pivots are the same as those of linear-move systems. The principal differences between these systems are the mobility of the inlet-end support tower (i.e., stationary or mobile), the mode of motion of the lateral (i.e., circular or linear/straight-line), and if there is a need for a separate guidance mechanism or not. These differences are considered not to have appreciable effects on the basic hydraulic principles governing flow in these systems and applicable equations. Thus, in practice, the hydraulics of these systems is considered identical.
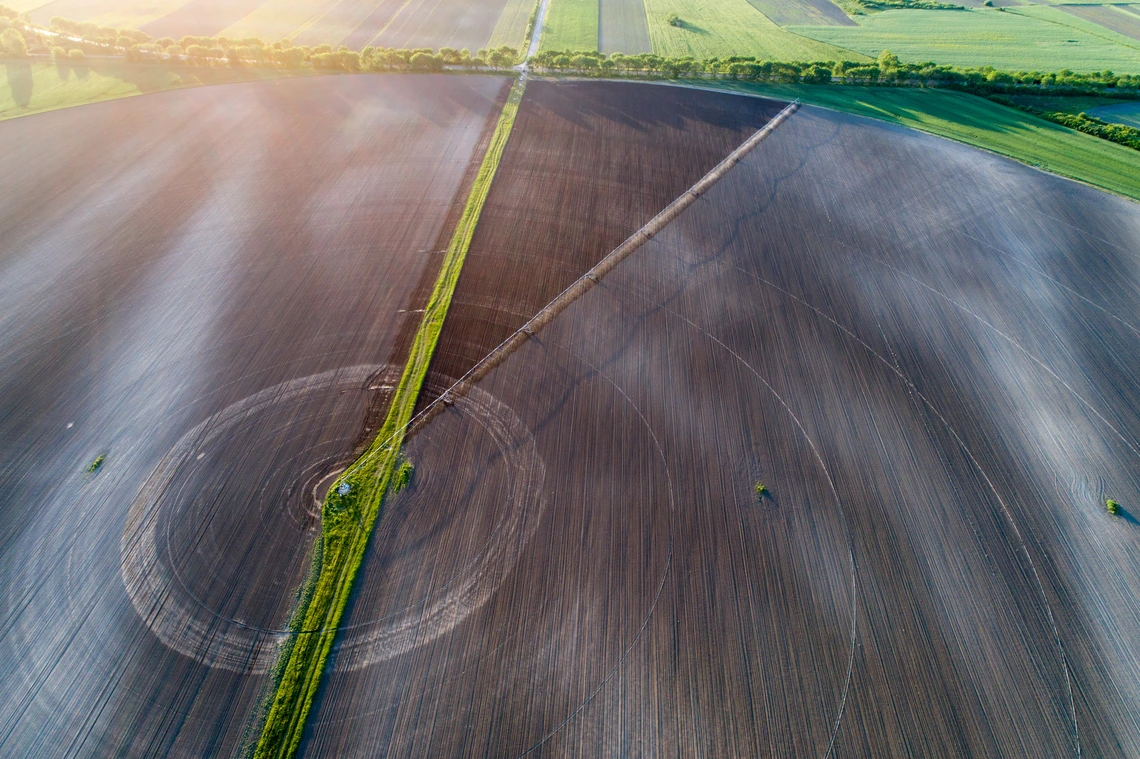
Figure 1. Aerial view of a center-pivot irrigation system irrigating a field
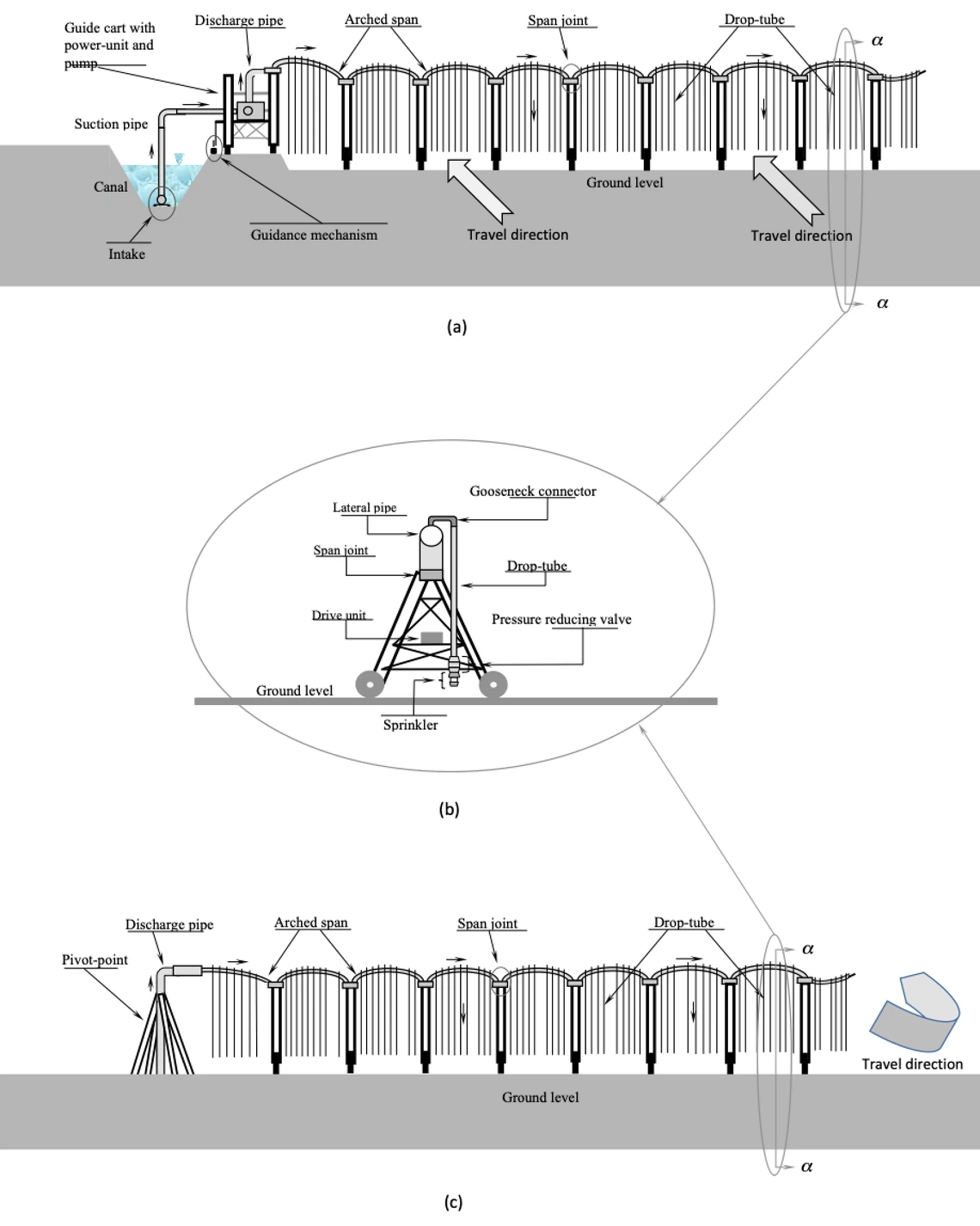
Figure 2. (a) Sketch of a linear-move system obtaining its water supply from a canal and (b) Details showing a support tower, drop-tube fitted with a prv-emitter assembly, and drive unit (from section at α-α,Figure 2a), and (c) Sketch of a center-pivot system. View larger
References
FRIS. (2008). Farm and Ranch Irrigation Survey. Volume 3 – Special studies part 1 – AC-07-SS- Washington, D.C. USDA National Agricultural Statistics Service. Available at: www.agcensus.usda.gov/Publications/2007/Online-Highlights/Farm_Ranch_ and_ranch_ Irrigation_Survey/FRIS.txt
Gregg, T. (2004) “Water Conservation Best Management Practice Guide.” Report 362, Texas Water Development Board, Austin, TX.
Keller, J., Corey, F., Walker, W.R., and Vavra, M.E. (1980). Evaluation of Irrigation Systems. In Irrigation: Challenges of the 80’s. Proc. Second Nat’l Irrigation Symp., 95-105. St. Joseph, MI, ASAE.
New, L and Fipps, G. (accessed 2020). Center Pivot Irrigation. Texas Agricultural Extension Service. Texas A&M University System. https://oaktrust.library.tamu.edu/bitstream/handle/1969.1/86877/pdf_1181.pdf?sequence=1&isAllowed=y
Martin, D.L., Denis, C. K., and Lyle, W.M. (2007). Chapter 16. Design and Operation of Sprinkler Systems. (eds. Hoffmann, G.J., Evans, R.G., Jensen, M.E., Martin, D.L., Elliott, R.L). 2nd ed, ASABE, St. Joseph, MI, pp.557-631.
Senninger (accessed 2017) “Pressure Regulator Guide.” (https://www.senninger.com/sites/senninger.hunterindustries.com/files/pressure-regulator-guide.pdf).